What are the Limitations of Using an ERP System? A Complete Guide for Battery Recyclers

Fred Fooks
CTO @ Gaea
Posted on 22nd January 2024
On this page:
- What are some of the challenges faced by battery recyclers today?
- What is ERP, and how is it currently used in recycling facilities?
- Five limitations of using a single-vendor ERP to manage battery recycling operations
- Best-of-breed solutions vs single-vendor ERP solutions
- Is an ERP solution expensive to customise?
- Why single-vendor ERPs may not mitigate compliance and regulatory risk
- How can Gaea help optimise existing ERPs for recycling facility management?
- Gaea supports you in three key areas:
- Key takeaways
The increasing adoption of electric vehicles (EVs) and renewable energy storage solutions has led to a surge in battery production. Battery recyclers now face a pressing need for digitalisation to meet rising demand.
According to a report by Grand View Research, “the global battery recycling market size was estimated at $1.83 billion in 2023 and is expected to grow at a compound annual growth rate (CAGR) of 37.6% from 2024 to 2030.”
As the global shift towards sustainable and environmentally conscious practices accelerates, battery recycling has taken centre stage. And whilst battery production has largely transitioned to full automation, battery recycling remains a manual process.
The efficient digitalisation of battery recycling is key for enhancing operational transparency, improving resource recovery, and aligning the industry with contemporary environmental and regulatory standards.
"Every day not digitalised is a day missing crucial data points that can inform future commercial and operational development. We all need to work together across the industry to make data a core pillar of recycling facility strategy."
George Postlethwaite, CEO at Gaea
What are some of the challenges faced by battery recyclers today?
The European Union has established an ambitious goal of achieving a 70% recycling rate for Lithium-Ion Batteries (LIB) by 2030. This target includes specific objectives like recovering 70% of lithium and 95% of nickel, copper, and cobalt from end-of-life batteries.
In the United States, facilities are anticipated to experience a significant surge in demand following the directives outlined in President Joe Biden's Inflation Reduction Act (IRA).
According to this mandate, by 2025, critical minerals present in the battery components of clean vehicles should not undergo extraction, processing, or recycling in countries identified as being 'of concern’.
However, despite these seismic changes, numerous recycling facilities are currently unprepared to cope with the escalating demand.
Many recyclers are still stuck managing facilities using spreadsheets, and urgent action is needed to digitalise battery recycling, which has traditionally been a very manual process.
What is ERP, and how is it currently used in recycling facilities?
ERP (Enterprise Resource Planning) systems, like Microsoft Dynamics, are pivotal in streamlining and optimising some key aspects of battery recycling operations.
In battery recycling, ERPs typically encourage the standardisation of processes. Most recyclers use an ERP for financial management, as ERPs are very useful for tracking revenues, managing procurement costs, and meeting accounting requirements.
If you are currently using an ERP to oversee your facility, you may have encountered limitations concerning the necessary level of complexity for warehouse and production management in battery recycling.
While ERP is a good solution for finance and accounting at any stage and size of a recycling facility, recyclers tend to quickly realise that further specialisation is needed to digitalise their warehouse and production processes.
In other words, digitalising complex battery recycling processes requires a more industry-focused solution to move your digitalisation journey from ‘Phase 2’ to ‘Phase 3’ (see chart below).
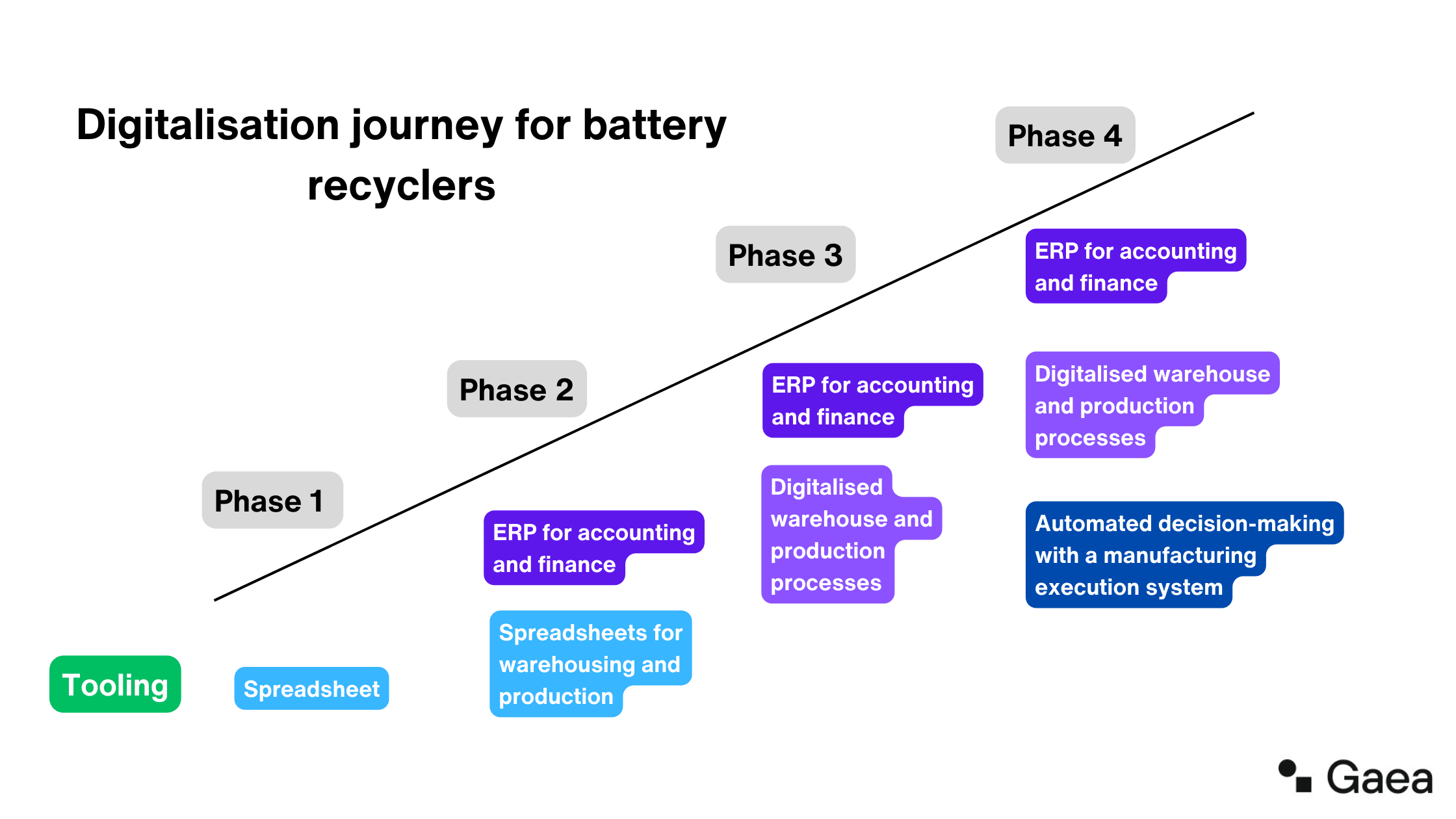
In ‘Phase 3’, recyclers encounter a pivotal decision: Adopt a generic ERP system with customisations OR opt for a vertical-specific solution tailored to their unique needs.
Five limitations of using a single-vendor ERP to manage battery recycling operations
Navigating the complexities of battery recycling operations poses unique challenges, and while ERP systems offer streamlined solutions, they come with inherent limitations.
- Generic ERP systems are hard for site workers to use and make data collection difficult
As ERP systems have features to meet every customer use case this makes the user experience a big challenge for site workers.
The on-the-floor operational system needs to fit seamlessly into the operational process to deliver key data points for recyclers to make decisions.
2. Limited support for material flow management
ERPs may struggle to effectively manage material flow, especially concerning mass balance in recycling operations.
The intricate tracing and handling of materials throughout the recycling process may not be adequately addressed, impacting inventory and production data accuracy.
3. Customisation is required to incorporate the production steps specific to battery recycling
Specific steps are involved in the battery recycling process, and to track the entire operation, these need to be digitalised.
The rigidity in accommodating specific production nuances could result in challenges, making it expensive and difficult to modify existing production processes within the ERP system.
4. Digitalisation challenges and reliance on spreadsheets
Despite being digital systems, ERPs may face challenges in complete digitalisation, leading to continued reliance on spreadsheets.
This dual-system approach can introduce complexities and data discrepancies and hinder the seamless flow of information, undermining the efficiency gains expected from ERP implementation.
5. Limited incorporation of user feedback
ERPs may not inherently incorporate real-time user and market feedback, potentially causing a disconnect between the system's output and current demands.
Without a dynamic feedback mechanism, recycling operations relying solely on ERPs may struggle to adapt swiftly to changing techniques and market conditions, impacting strategic decision-making.
Best-of-breed solutions vs single-vendor ERP solutions
Existing ERPs offer generic warehouse and inventory management modules that lack customisation for the distinct requirements of battery recycling.
The user experience for key users in this field poses a challenge, as these modules do not cater specifically to the nuanced demands of battery recycling operations.
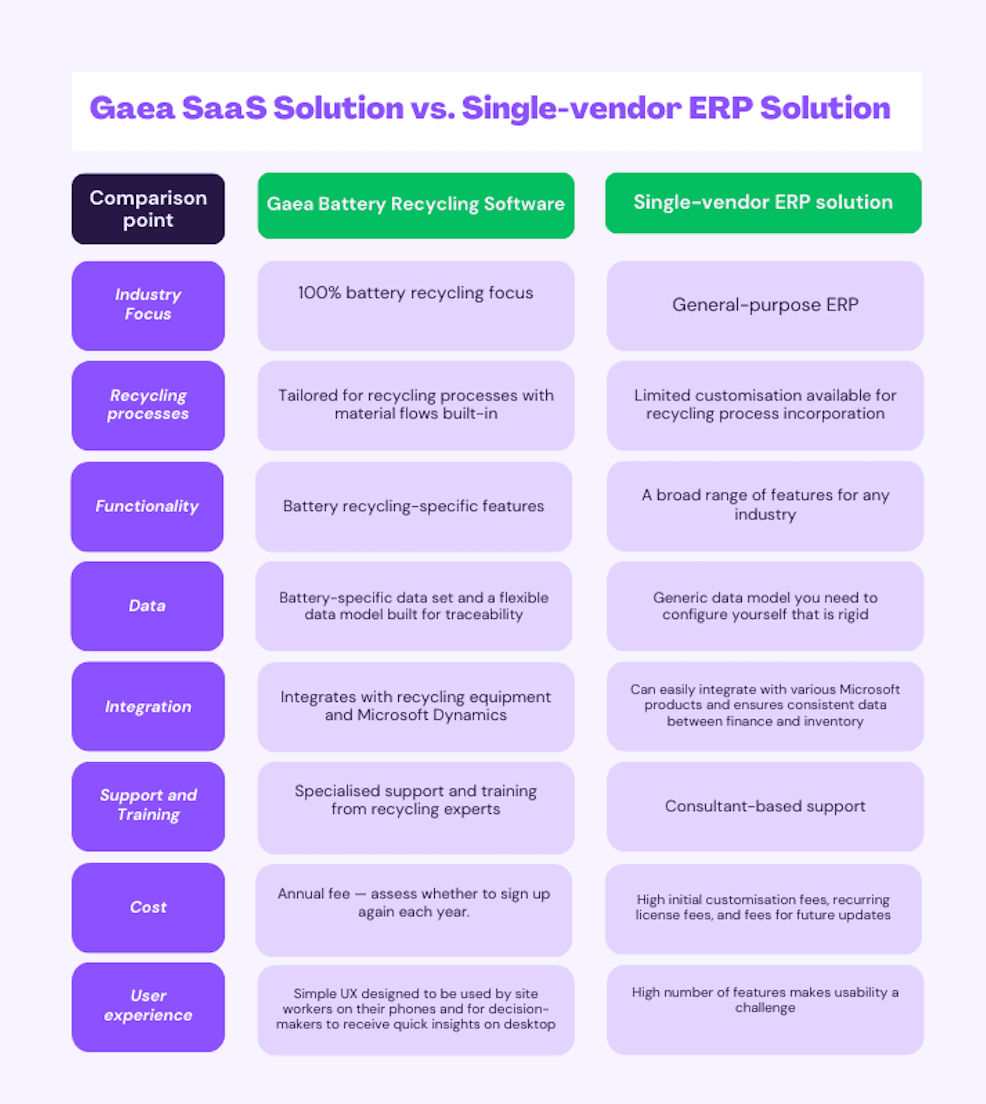
There are systems already on the market for pricing and battery cell data that when integrated will deliver a better solution than generic ERPs for battery recyclers. Generic ERP systems put the integration pressure on companies vs. having integrations ready off the shelf. To stay ahead of the market the latest integrations are required.
The complexity of recycling demands a best-of-both-worlds situation: a fully integrated ERP system with vertical extensions.
Is an ERP solution expensive to customise?
Integrating a vertical Software as a Service (SaaS) solution into an existing ERP system, as opposed to customising with consultants, offers several advantages for organisations, particularly in complex industries like battery recycling.
However, one key advantage is cost-effectiveness, as customising an existing ERP is usually expensive.
This expense is because if the ERP has an upgrade, you likely need to rewrite many of the updates you’ve made. In other words — there is often a hidden maintenance cost associated with builds of this nature that can reoccur annually.
This is because vertical SaaS solutions, like Gaea, often follow a subscription-based model and reduce upfront costs. In contrast, extensive customisation with consultants can be resource-intensive and may lead to higher initial and ongoing expenses. SaaS solutions offer a predictable and potentially cost-effective pricing structure.
You become liberated from the hassles of software updates and maintenance.
Why single-vendor ERPs may not mitigate compliance and regulatory risk
The UK government is pushing to address concerns about environmental impact, potentially leading to a mountain of admin for battery recyclers. For example, the UK government is set to introduce mandatory digital waste tracking from April 2025 as part of its broader Resources and Waste Strategy for England.
While generic ERP systems offer basic compliance functionalities, they often need help managing the specific regulatory challenges unique to battery recycling. The rigidity of single-vendor ERPs can lead to significant gaps in compliance tracking and reporting, especially regarding the granular details required for material traceability, waste management, and environmental impact assessments.
Gaea provides built-in reporting tools that are aligned with industry-specific regulations. The platform is continuously updated to reflect the latest regulatory changes, helping recyclers avoid compliance risks.
These gaps increase the risk of non-compliance and expose your business to potential fines, legal liabilities, and reputational damage.
How can Gaea help optimise existing ERPs for recycling facility management?
Gaea functions as a specialised operational layer designed for battery recycling. It integrates with your ERP system to efficiently gather essential information throughout the recycling process.
Gaea’s primary purpose is to simplify the tasks of battery recyclers by offering a straightforward user experience.
Gaea supports you in three key areas:
- Effortless warehouse management
Gaea supports inventory scanning across the warehouse using QR codes, ensuring accurate and real-time updates. Thanks to Gaea's user-friendly interface, you can conveniently use the camera on your smartphone or tablet to perform scans from any location, providing a secure and simple way to check in batteries. - Optimising production management
A commonly cited challenge in production is training facility workers to consistently follow a process and adapt to various battery types, especially those used in EVs, given the wide variety of chemistry types.
Gaea provides a detailed tracking system that helps ensure processes are simple to follow, avoid bottlenecks, and optimise workflows. This creates more consistency and reliability in the production process, enhances compliance and safety, and sets you up to run your processes at scale. - Delivering enhanced insights
Recyclers encounter multifaceted challenges in obtaining crucial insights, such as predicting the profitability of processed batteries, determining optimal material pricing, and ensuring high-quality services amidst varied input feeds and capacity management difficulties.
Gaea revolutionises the landscape by delivering detailed analytics and customised reports, transforming raw data into actionable insights. These tools empower you to navigate operational complexities, comprehend financial performance, and make informed decisions, ultimately enhancing your efficiency in the recycling process.
Key takeaways
Choosing Gaea as your vertically integrated SaaS solution alongside your existing ERP offers a strategic advantage in multiple ways:
- Cost-effective
Gaea limits the need for extensive customisations and allows you to leverage off-the-shelf solutions tailored to your specific needs as a battery recycler. - Purpose-built
The quality of the product aligns seamlessly with your goals, offering a purpose-built solution rather than a generic one-size-fits-all approach. - Highly adaptable
Gaea's constant updates ensure that your solution evolves with the ever-changing landscape of battery recycling, providing a forward-looking and adaptable platform compared to solutions stuck at a static time.
Working with Gaea streamlines your battery recycling processes and positions your operations for sustained efficiency and growth.
Want to learn more about how Gaea helps battery recyclers? You can read about why we founded Gaea here.
Want to learn more?
Get in touch with us to learn more about how Gaea can help your business.